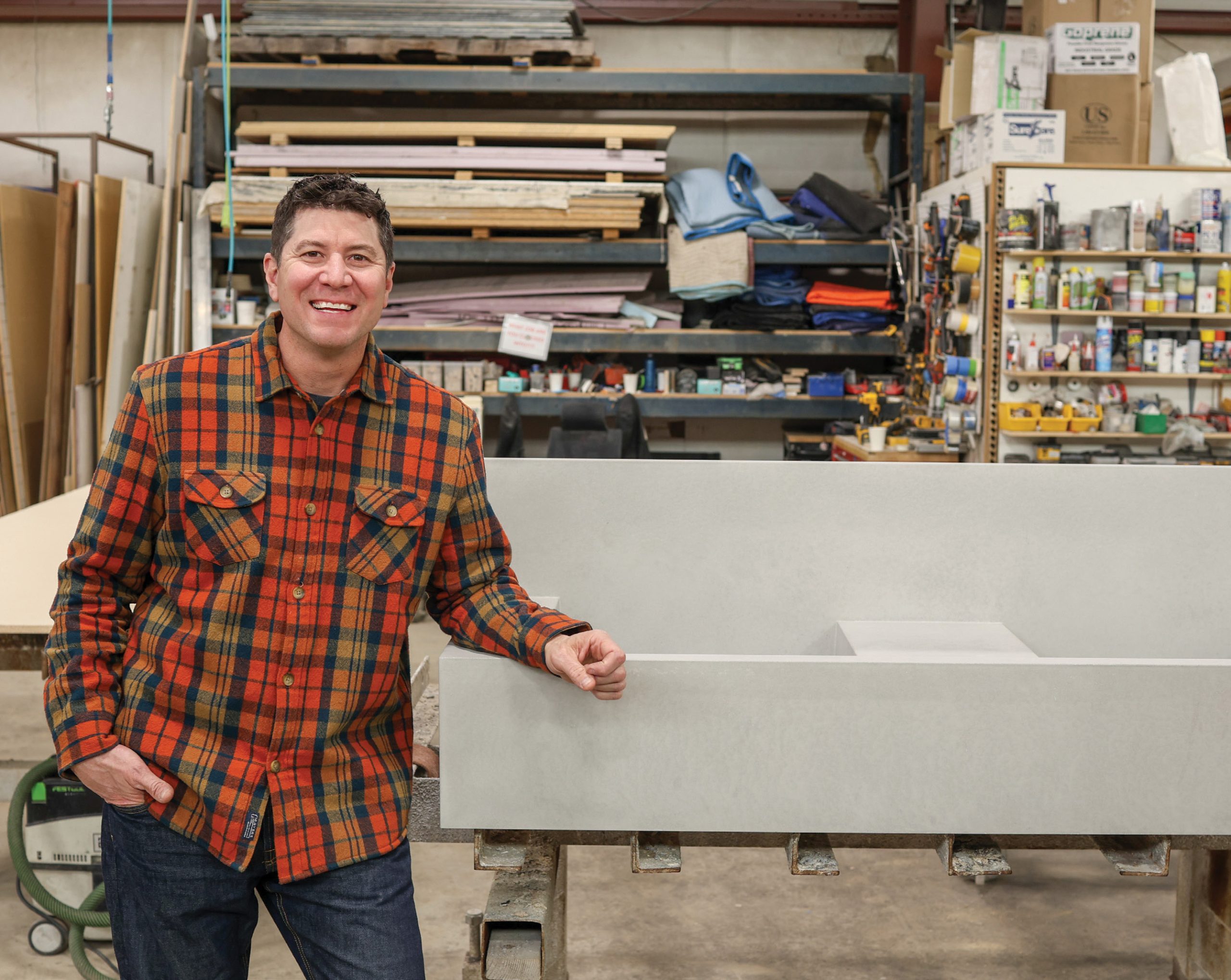
03 Apr TIMELESS METHODS: CAST STONE
inConcrete is probably not the first thing that comes to mind when people conjure up a dream home. But for Jerrad Inlow, founder of Bozeman-based Elements Concrete, working with concrete, wood, and metal is art. And the architects, builders, and designers in the wide triangle around Big Sky, Park City, and Jackson Hole agree.
While Elements Concrete is renowned for its sleek, seamless sinks, vanities, countertops, and interior and exterior veneers, the firm is also known for its woodworking and unique integration of metals like steel and copper into project designs. In this, Inlow is considered one of the best in a burgeoning transformation of concrete, from structural component to decorative art.
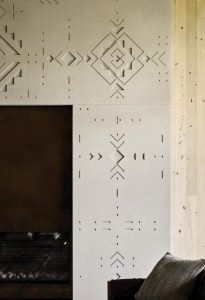
The fireplace surround in this Wyoming home was designed in collaboration with the client’ tattoo artist, and many of the mold pieces were different levels, enhancing the piece’s dimensions. | PHOTO BY MATTHEW MILLMAN
Inlow’s mother was a professional ceramicist with a home studio, and Inlow loved the medium, often traveling with her to trade shows. But when the time came to decide about his future, he majored in business at Houghton College in New York.
“The idea of selling mugs at $10 a pop didn’t seem like much of a career opportunity,” he says, adding that he spent most of his college years in the art studio anyway. After graduating in 1998, he found himself somewhat adrift, in search of a job that would be fulfilling. Then, a friend of a friend introduced him to concrete.
“I was still really into ceramics,” Inlow says, “and I saw concrete as a similar medium — to be able to work three-dimensionally and to create functional art. And it gave me more of a potential to make a living.”
After briefly partnering in a cabinetry business, Inlow started his firm in New Jersey, working in New York City and the Hamptons, often on commercial projects for companies like Anthropologie and Urban Outfitters.
An avid snowboarder, Inlow frequently vacationed in Montana, where he had relatives and fell in love with Bozeman. “I thought, if you can live where you vacation, then you should absolutely do that,” he says. So, at the height of the 2008 recession, he picked up and moved to Bozeman to start again from scratch.
In a way, he now sees the recession as a blessing. He was able to introduce himself to architects and designers who suddenly had all the free time in the world, and when business picked up again, he was in on the ground floor.
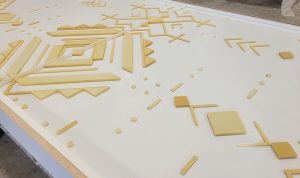
The completed work on the fireplace was meticulously aligned to match the drawings. The small parts are custom-cast rubber that were carefully removed after the casting. Both processes were extremely time consuming. | PHOTO BY ELEMENTS CONCRETE
“Everything we do is made to order,” he says. “Everything from color to texture to shape, and we make prototypes. We’ll generate a mini version and send that over for approval, working with the architects and designers throughout the process, getting exactly what they want.”
“He does a lot of decorative concrete work for us, mostly in lieu of stone,” says Scott Payne of Farmer Payne Architects. “What’s really cool about the products he’s using, like at my house personally, is that we can do a lot of integrated things. For example, my powder room: It’s a pour of concrete that becomes the countertop, sink, basin, drain — everything. So, it’s timeless in that it’s minimal, and there’s not a lot of parts. I guess monolithic would be the word. He has very progressive ways of building a solid piece, so it reads as if it’s a foot thick, but in reality, it’s 2 inches.”
“Some of the most difficult pieces we do don’t always look like the most difficult,” Inlow says. “Trying to make something look simple can be very complicated for one reason or another — because of the design or, in some cases, functionality.”
Recently, Inlow shaped a massive fireplace surround that the owner wanted to model after the tattoo on his back. He worked not just with the architect and builder but with the tattoo artist as well. “It was very technically difficult, a lot of shapes and ins and outs,” Inlow admits. “It took a lot of time and energy, but it’s an amazing-looking piece.”
While the high quality of Elements Concrete’s work is well established, Inlow’s innovations set the firm apart. He’s a restless guy, describing himself as having an artist’s ADHD urge to mix things up. Currently, he’s working on cast-in-place board-form concrete veneers for both interior and exterior applications. He recently completed a project that amounted to 6,000 square feet poured right at the property. Again, the finished product looks like a solid wall but is mere inches thick.
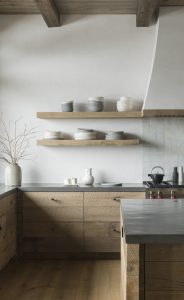
These hand-troweled kitchen counters have beautiful imperfections, highlighting the honesty of the material. If you run your hands over the surfaces, you feel slight undulations. It’s one of many finishes proving the versatility of concrete. | PHOTO BY AUDREY HALL
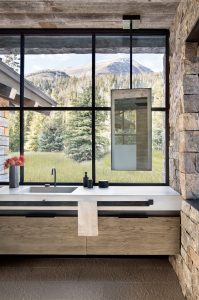
A double primary bath vanity has integral sinks and an integrated towel bar. Concrete sinks are right at home in the Mountain West, and there’s no limit to size, shape, thickness color, or texture. | PHOTO BY GIBEON PHOTOGRAPHY
“It’s a pretty unique product, and we’ve been getting good feedback from builders and architects,” he says. “It solves a lot of the problems they have with traditional board form, which is like a 12-inch-thick wall. Sometimes builders and architects have to run plumbing and electricity through there. Our product allows them to build a traditional wall; we come in after the fact and pour our veneer. Our mix design allows us to pour in a very thin space, so it’s unique in that aspect as well. There are other companies that offer sheets or planks cast in their shop, and then they have to be installed like tile. So, our process allows us to pour infinitely large panels, and you’ve got a far superior product.”
He calls another element he’s working on “modified rammed earth.” His parents are missionaries who built a school in Tanzania, where Inlow helped on various construction projects and where he first discovered rammed earth, which he describes as “bonkers. Nothing is more beautiful. It’s such a work of art. It’s truly amazing.”
But traditional rammed earth doesn’t survive the elements of the Mountain West, he explains. “We’ve created a modified version that will survive our harsh winters and also be suitable to design into a veneer-type application. It’s quite cool: It looks exactly like traditional rammed earth, but it’s far more durable.”
As an architect, Payne is strongly committed to design that’s timeless, often employing natural materials in his work — although certain manmade materials, like concrete, steel, and glass, nicely fit that ethos as well.
“Jerrad’s product is so much better than everybody else’s,” Payne says. “We’ve had other products that chip and break, and there are a lot of people out there who do concrete countertops, but his are, to me, more like stone. People come in and say, ‘Oh, I didn’t even realize that that’s cast concrete.’ So, we call it cast stone. It’s the quality of the product and the quality over time.”
And, when an architect chooses a firm to work on his own home, that firm must have something distinctly special to offer.
Laurel Delp is a regular contributor to Western Art & Architecture, A Rare World, Town & Country, Travel + Leisure, and many more.
No Comments