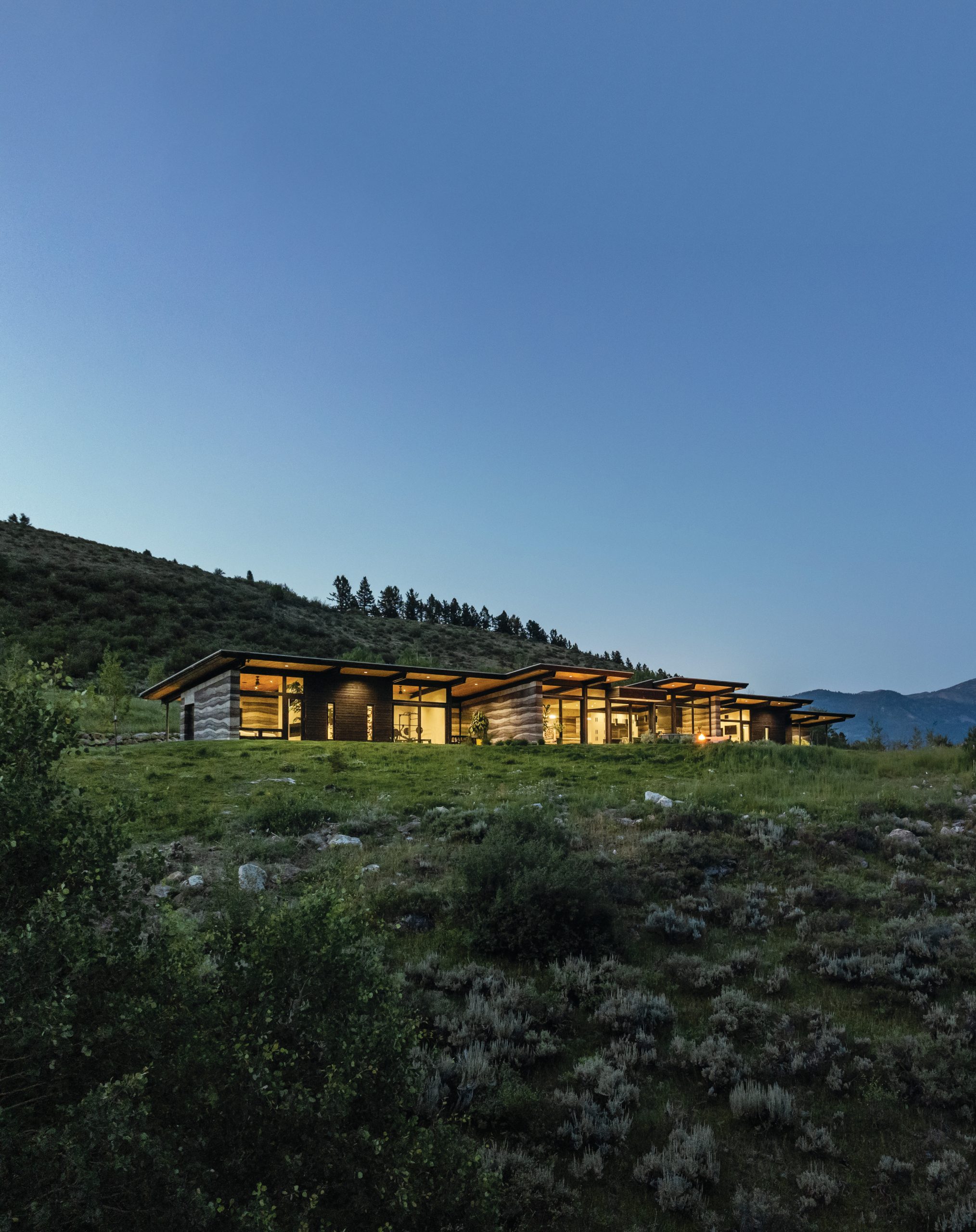
03 Apr RAMMED EARTH FOR THE 21ST CENTURY
inARCHITECTURE | Ward | Blake Architects
CONSTRUCTION | Ormond Builders
Rammed-earth construction has taken on various iterations, long serving to shelter humans across the globe. Despite its popularity through the ages, it is seldom seen in the Northwest. But architect Tom Ward of the Jackson, Wyoming firm Ward | Blake Architects is endeavoring to change that.
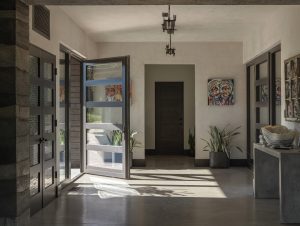
This rammed-earth home by Ward | Blake Architects in Freedom, Wyoming is oriented toward the south to capture the sun’s energy during winter days and release its warmth at night.
A technique that, in its simplest form, consists of banging together a pair of wooden forms then pounding together dirt and sand between them, rammed earth is a natural, layered medium that becomes rock-hard, resists water, and absorbs solar warmth. Versions of the construction method can be seen in the Southwest’s adobe bricks made of straw and compressed mud, and as Ashley Nicole Gramlich notes in her comprehensive 2013 University of Oregon historic preservation thesis, there’s ample evidence of pisé de terre in China, Europe, and elsewhere. The process was first documented in Western civilization by the Roman philosopher Pliny the Elder in about 79 AD, while in more modern times, rammed-earth buildings were under construction during the Jeffersonian era, the Great Depression, and the back-to-nature movement of the 1970s.
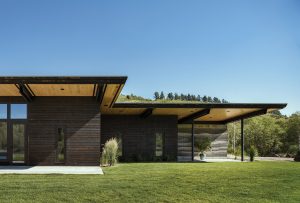
Designed for passive solar, the 85-foot-long home features exterior overhangs to protect it from summer heat.
In 1980, Mother Earth News published a feature article called “Living in Rammed Earth Houses.” The magazine championed the work of David and Lydia Miller, who’d resided in rammed-earth homes since 1945. The couple had discovered the “building with soil” process in a 1937 copy of American Home magazine. Then, they followed it up with trips to Europe and correspondences with English and German architects who’d worked the process successfully.
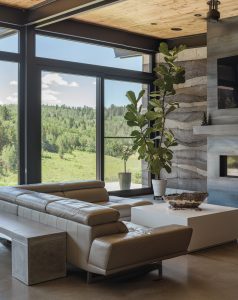
The living room windows look to views of an adjacent valley and canyon wall.
Alas, these structures were not popular. As Gramlick wrote, these energy-efficient, if labor-intensive, homes were usually deemed marginal or fringe. “This is true even though at times the U.S. government has been a proponent of alternative building techniques, especially rammed earth,” she explains.
Fast forward to 2004, when, after decades of hands-on investigation, Ward patented a post-tensioned rammed-earth process he calls “Earthwall.” He’s completed three homes and a children’s learning center with the technology so far. The newest iteration is a 6,280-square-foot home on a south-facing knoll of a 160-acre site in Freedom, Wyoming. “It’s all undeveloped except for this house on the site proper,” Ward says. “It’s so wild — it fronts a small creek and valley and an untouched slope.”
He set up the home’s design for passive solar, with overhangs to protect it from summer heat. In winter, its concrete floors and rammed-earth walls absorb warmth all day, then release it at night. In essence, it’s an extension from Ward’s studies at Arizona State University, which was, in the late 1970s, the nation’s leader in solar applications.
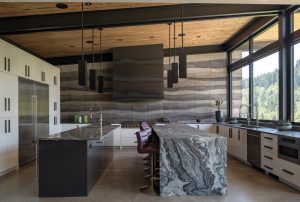
In the kitchen, exposed rammed-earth walls are complemented by a waterfall island composed with a striated-stone surface.
The new home also benefits from Ward’s early conversations with a structural engineer about his experience examining damage in an earthquake’s aftermath in Turkey. Later, Ward would conduct years of testing and re-testing. He intentionally built walls designed to fail in order to examine their actual mode of failure. He wanted to prove his theory on rammed earth and post tension, so he demonstrated it in a low-tech experiment in which 12 inexperienced friends assisted him. “It was actually a lot of fun,” Ward says. “A local ready-mix plant was willing to mix it up for consistency, load to load.”
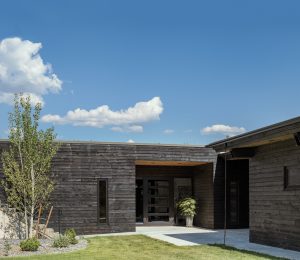
Outside, the gray tones in the rammed-earth walls relate directly to weathered lava flows on adjacent hillsides.
Finally, Ward published an academic paper, and a few years later, Earthwall was a bona-fide process for building stabilized rammed-earth homes.
“It’ll outlive anything made of wood,” he says. “It’s as resilient as concrete.” The 10-percent-cement content is key: “It’s a reinforced concrete wall that resists lateral forces, which is what earthquakes do.”
Post-tensioning rods — tensioned to about 14,000 PSI — are placed in plastic sleeves to prevent any mechanical bond with the rammed earth. That protects the walls from falling out of plane. “It keeps wall forces vertical, to utilize the rammed earth for what it’s good at — resisting compressive stress — with these forces running down through the walls and resolving into the footings,” Ward explains.
The West, especially rural Wyoming, is no hotbed of rammed-earth construction. So, when Greg Hostert of Ormond Builders in Idaho Falls, Idaho was named project manager for the build, he and his crew got a crash course from the architect in the technology.
While Ormond Builders was familiar with rammed earth, the team hadn’t worked with it previously to this project’s scale. “Tom Ward has rammed earth in his home — and he said, ‘I have the knowledge, and I know you guys can do it,’” Hostert recalls of early conversations.
Structural steel, glulam beams, wood timbers, and heavy foundations typical of the residential construction Hostert completes in Jackson and Sun Valley are increasingly becoming de rigueur. But, with a team of multitaskers capable of welding, framing, and swinging a hammer with the best of them, Hostert wasn’t afraid to accept the challenge of a new medium. “It’s not the typical 2-by-6 stick-frame house,” he says. “There are much larger openings for windows and door sizes that require more steel structure.”
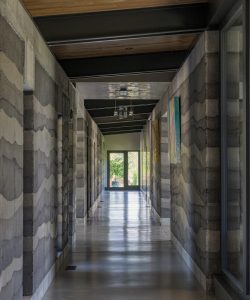
The main corridor is where the architect and builders primarily used the white, black, and gray rammed earth, though it’s featured in the primary suite and elsewhere in the house as well.
Once Ward walked the builders through the material and process, they made sample walls. The clients chose black, white, and gray as primary colors for the rustic, natural look of basalt that reflects the weathered lava flows on adjacent hillsides.
Then, Hostert and his team got to work on forms and walls. First, they built a 12- by 12-foot “rat slab” for a clean, durable surface on which to mix the rammed earth. “From there, it was a tedious process of mixing aggregate, sand, concrete dye, cement powder, concrete adhesive, and a very limited amount of water,” he says. “The material was mixed to a consistency that would form a ball in your hand, but if you dropped the ball it would begin to fall apart before it hit the ground.”
Once mixed to the proper consistency, they moved the aggregate to the forms with a front-end loader. In the forms, a pneumatic pogo stick mechanically compacted the medium, as workers kept track of the interior patterns by observing outer ties in the forms. “Once a lift was compacted and cured, the process started over again,” explains Hostert.
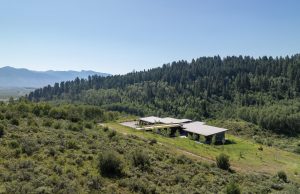
The home is sited on the south knoll of the property and fronts a small creek, a valley, and an untouched slope.
When all was said and done, the builders realized the architects’ intent to create a rigorous design that used every aspect of the environment and satisfied the clients’ needs.
Those needs included taking advantage of the spectacularly wild qualities of the site. “[The site features] are captivating,” Ward says. “They informed innumerable aspects of the design, from the way the house sits on the site to the general orientation of the home to the use of materials.”
As luck would have it, the site’s most beautiful exposure was toward canyon walls to the south, which also offered the most manageable orientation for solar control. That meant the architects could place most of the home’s glazing to face the best vistas while capturing the sun’s energy in winter months. “It led to a very simple design, with all rooms commanding great views and orientation,” says Ward. “It turned out to be a fantastic experience. You can view bears, mountain lions, elk, and deer from the comfort of the living room or its attendant patio.”
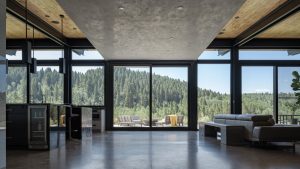
The living area opens up to an attendant patio, where bears, mountain lions, elk, and deer can be seen from the comfort of a sofa or chair, inside or out.
The views from above the 85-foot-long home are nothing to scoff at either — and they’re accessible. A relatively low-sloping roof, at an angle of 2/12, is layered with a PVC membrane. A deck laid in Ipe wood atop a series of composite pedestals runs down its center. “The clients loved the views and wanted to be able to sit up there in the evenings,” explains Hostert.
Overall, the architects and builders created a sophisticated home that honors its surroundings thanks to a persevering Ward, who is bringing an ancient building method up to 21st-century codes.
J. Michael Welton is the author of Drawing from Practice: Architects and the Meaning of Freehand (Routledge, 2015). His articles have appeared in The New York Times, The Washington Post, Metropolis, Dwell, and The News & Observer in Raleigh, North Carolina. He is editor and publisher of the digital design magazine architectsandartisans.com.
No Comments